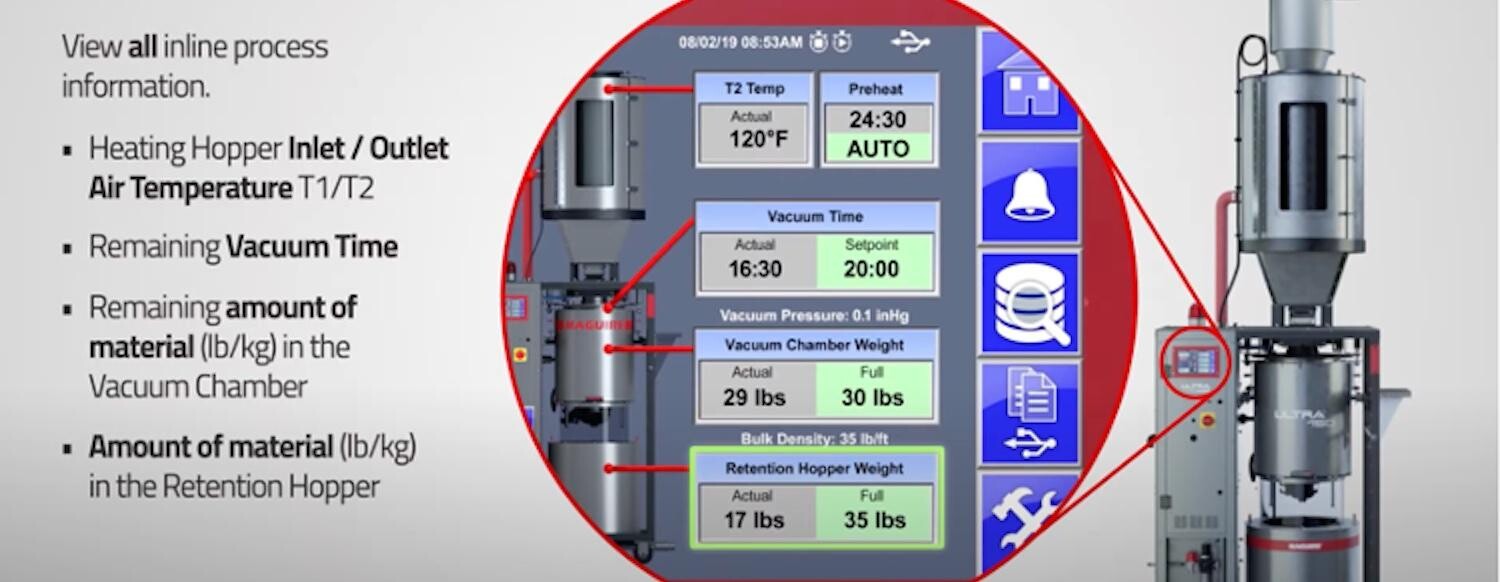
Maguire ULTRA Dryer - Advancing the Drying Process in the Era of Digitalization
(Maguire, Aston, PA, October 12, 2021) … Since Maguire first launched the Vacuum Dryer in 2000, several generations have been produced bringing unique benefits to plastics processors. Processers now benefit from faster drying times and the highest level of drying management and control of the entire drying process. The Benefits of Vacuum Drying vs Desiccant DryersThe unique patented vacuum design, (most recent patent #10751918 gr... read more